The choise of
Responsible Growth
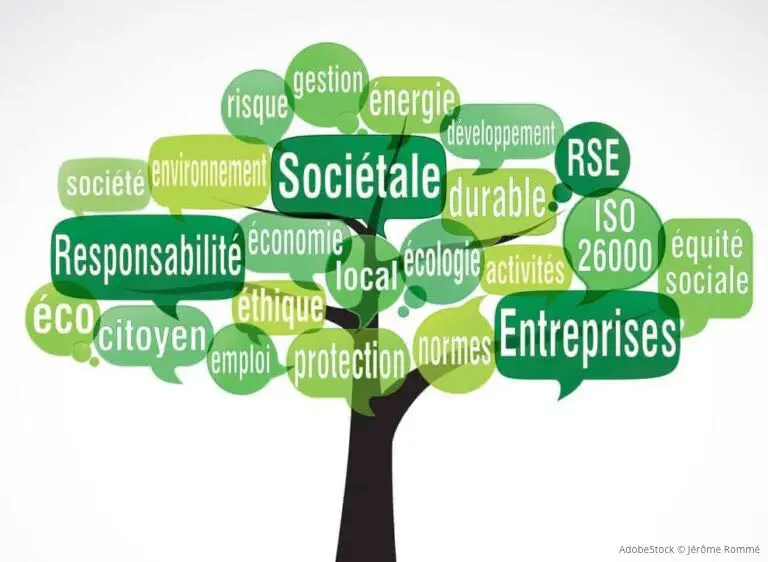
In 2011, Porter and Kramer proposed a paradigm shift regarding Social and Environmental Responsibility: With the introduction of the concept of Shared Value Creation, CSR could be considered not as an artificial constraint disconnected from the company’s growth and profitability objectives, but as a factor of competitiveness, with the company relying on its resources and skills to create economic value as well as social and environmental value.
Ten years later, sustainability has become a key element of differentiation and success for companies in their interactions with all stakeholders: customers, suppliers, employees, the State and… shareholders. Whether it is to sell products or services, to attract and retain talent, or to attract capital, the commitment to a responsible approach is becoming essential and is perceived as a vehicle for progress: isn’t the opposite of sustainability obsolescence?
Like the digital revolution that began 20 years ago, the principle of responsible growth represents a radical transformation whose spread throughout the entire economy is accelerating. New opportunities will certainly arise from this, but many companies – large and small – will also have to face profound changes that question their business model and their sustainability. In order to better support its portfolio companies in this transformation process, Sparring Capital has decided to create a “Sustainability Manager” role, and to entrust it to a specialist in the implementation of CSR policies, in charge of intervening alongside the front office investors. This newsletter is an opportunity to get to know him and the new Sparring Capital recruits. It also discusses the concept of Lean Durable® (Sustainable Lean), created and supported by Pop, the latest investment of the SC Fund 2. Pop or the demonstration that the quest for operational excellence can only produce sustainable results if it puts people at the heart of the process.
May this approach have a bright future ahead of it…
The Sparring Capital Team
Lean Durable Interview
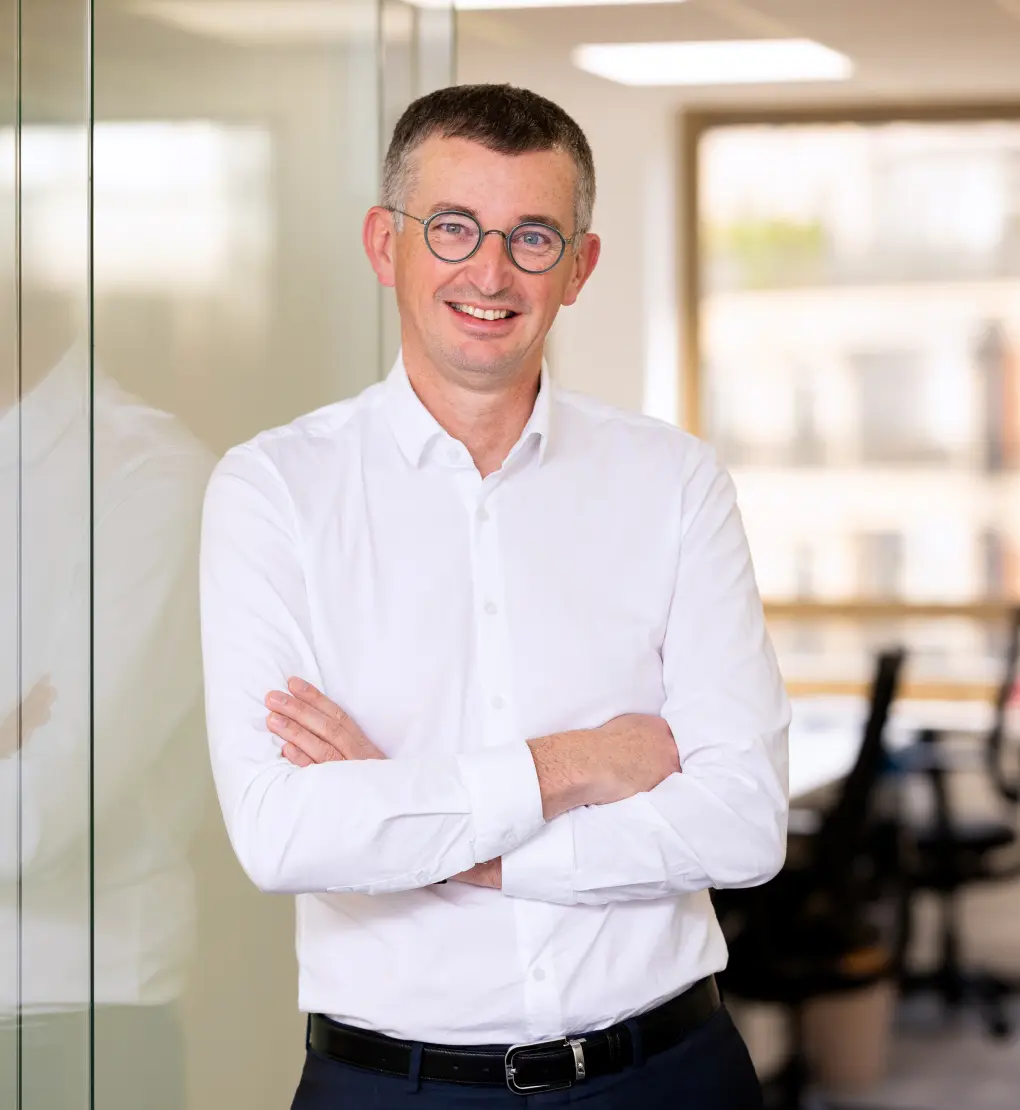
Frédéric Stoll – Associate Director, POP
Could you define Lean Management?
Lean Management is originally a management and work organisation method based on the collection of factual data from the field to optimise the operational management of the company. This approach, created after the Second World War by the automotive sector (inspired by the Toyota production model), has shown its effectiveness on economic results (industrial profitability) and on the level of product quality. Today, Lean has become a fundamental cornerstone of corporate management. It aims to involve all the players in an organisation on a daily basis in order to identify, qualify and solve issues (called “waste” which make operational processes less productive). We talk about reducing non-value added time such as waiting for parts, lack of decision making, work to be redone, unnecessary operations and especially over-production that monopolises resources to build up too much inventory. Finally, we speak of a “Lean approach” when the management of a company decides to structure a continuous improvement process in its medium/long term strategy. Lean then makes it possible to ensure the satisfaction of the customers by the permanent search for the best quality at the best price. It also ensures that employees work in better conditions.
What are the advantages of Lean Management for companies?
In our opinion, Lean Management is the main vehicle for sustainable performance for a company. It makes it possible to obtain very short-term results from both a quality and profitability point of view. And if it is applied with strong managerial values, it gives meaning to the work of each employee. On a day-to-day basis, Lean makes it possible, through its collaborative approach, to solve “irritants”, those recurrent operational anomalies that annoy and stress employees at their workstations. We understand that Lean, when used properly, is also a vehicle for better communication within a team and contributes to improving social relations. Thus, Lean will make it possible to continuously improve the triptych essential to the development of any company: customer satisfaction, employee well-being and economic profitability.
What type of company does Lean apply to?
Initially deployed in industry, in the mass production automotive sector, Lean Management is now applied in all areas of the global economy. We speak of “Lean Manufacturing” when Lean is applied in industry and of “Lean Office” when it is deployed in tertiary activities such as banks, hospitals, insurance or any other service companies. Today, the Lean methodology is applied in all sectors (industry/services), from large international groups to very small companies and for companies supplying products or services in large/medium/small series or working in a totally customised way.
Lean durable®:
Which observation made you want to develop the notion of Lean durable®?
Lean Management was misused by some companies in the 1990s and 2010s. They used this methodology as a simple method of brutal “cost-killing” without taking into account its fundamental cornerstone which is the involvement and recognition of the personnel. Moreover, at that time, the environmental aspects were totally underestimated in the method. In these companies, we saw significant but unsustainable short-term economic gains and a demotivated workforce. At POP, we decided to challenge the Lean methodology with the aim of returning to the fundamentals of the approach and thus moving towards sustainable performance, which is both a source of employee fulfilment and a guarantee of economically responsible gains. In concrete terms, we have developed the tools of the methodology by integrating a human dimension and we lead our clients to integrate the global performance approach (Client/Employee/Environment). Since 2012, we have registered the “Lean Durable®” trademark, a guarantee of seriousness for our clients.
What are the main characteristics of the Lean Durable® approach?
Lean Durable® is operationally reflected in three components:
1. “Strategic Lean” enables Top Management to structure its continuous progress approach over time and to communicate its commitment to stakeholders (customers, employees, suppliers, local players, etc.). In this sense, Lean Durable® contributes to the company’s CSR dynamic.
2. The global performance cornerstone focuses on the deployment of Lean production tools, the reduction of waste and variability, and the improvement of quality. This cornerstone is carried out in the form of collaborative progress projects, carried out in the field with the players concerned. It aims to simultaneously optimise the main performance criteria (team well-being/quality/time/cost/environment).
3. The cultural dynamic of continuous progress enables each operational manager to build a lasting relationship with his or her team based on respect, daily communication and visual management. This last component takes the longest to deploy, but it is the key to the sustainability of results. It is also, in our opinion, the most rewarding for the team.
How does the sustainable approach impact the way Pop’s teams do their job?
Before joining us, POP consultants had acquired strong experience (minimum 8/10 years) in Lean but also in operational management in industrial or service companies. In our opinion, this is an essential criterion for supporting companies in their Lean Durable® transformation. In 2011, we built the POP school: a “factory school” based in Nantes. It is a real factory making skateboards and a showroom for Lean Durable® best practices. This educational tool, unique in France because of its global approach (Lean manufacturing, Lean office, Lean strategy) is a place of learning in which our trainers help our clients discover Lean tools and show them the subtleties of making their continuous improvement approach sustainable. All our consultants are trainers and work both at the POP School and at our clients’ sites. They thus personalise their training sessions to make their missions in companies more effective. More generally, we wanted to deploy the Lean Durable® approach for our own internal activities. All our employees are thus involved in the daily rituals of exchanges and problem solving. Autonomy is the order of the day and is a source of motivation and personal development for the teams.
Are the benefits of the sustainable Lean approach measurable in concrete terms? What are the performance indicators that are most positively impacted by the sustainable approach?
Yes, every company can concretely measure the benefits of a Lean Durable® approach. The construction of performance indicators is an integral part of the methodology. The KPIs are customised in order to best meet the expectations of the teams and management. We build them and make them consistent between the different hierarchical levels of the company. Classically, we will find operational and financial KPIs such as the customer satisfaction rate (deadlines, quality), profitability (productivity, material yields, margins, etc.), supplier performance (service rate, ”Right first time” etc.), but also the employee well-being rate (team weather report, presenteeism, ergonomics, feedback, etc.), and finally the environmental aspects (energy consumption, waste, scrap, etc.) It is important to remember that we co-construct with each client its own indicators that will enable it to measure the progress of its sustainable performance.
Is it possible to link Lean Management and the CSR approach?
We believe that a Lean Management approach, deployed according to the sustainable approach recommended by POP, is an integral part of a company’s CSR approach. The purpose of Lean Durable® is to work on the expectations of the company’s various stakeholders and to guarantee their satisfaction over time while minimising the resources it consumes. This is my definition of CSR.